[ad_1]
The Valence plant will produce 150 million sq. centimeters of energetic floor space of OPV modules utilizing its inkjet printing know-how, with the objective of quadrupling its capability by 2026. Sensitive to pure and synthetic gentle, Dracula’s modules operates indoors from any gentle supply and supposed. to be used in IoT, industrial electronics and as battery replacements.
Dracula Technologies inaugurated the natural photovoltaic (OPV) module manufacturing line in Valence on September 12. With about 40 workers, seven patents filed, the primary industrial contract and bold tasks in growth, the corporate applies the “lab to fab” precept: an preliminary growth section primarily based on laboratory analysis, adopted by funding in industrial gear to place the innovation into manufacturing.
What is particular about Dracula Technologies modules? They are delicate to pure and synthetic gentle, and function indoors utilizing any gentle supply. Dracula’s modules might be finest used as battery replacements in distant controls, small industrially related gadgets, sensors and even digital chips in industrial or logistics facilities.
The Green Micro Power Factory now has a manufacturing capability of 150 million sq. centimeters of energetic floor space of natural photovoltaic modules. The manufacturing relies on inkjet printing know-how developed by Dracula throughout 12 years of analysis. Because they’re printed, the modules can take any form with out extra manufacturing prices and might be tailored to satisfy energy necessities.
OPV: Finding the proper technological and industrial method
The precept of OPV know-how relies on the affiliation of a semiconducting polymer (donor) with an natural materials (acceptor), which collectively kind the energetic layer. The energetic layer absorbs gentle after which converts it into vitality by creating bonded electron-hole pairs (excitons) that transfer till they attain the donor/acceptor (D/A) interface, the place cost separation happens. . The remoted cost carriers go via this energetic layer till they go via the photo-active layer, the interfacial layers after which the electrodes to succeed in the exterior circuit.
Dracula Technologies makes use of the idea of quantity heterojunction, the place the energetic layer consists of a heterogeneous combination of donor and acceptor, which permits a really extensive D/A interface to be constructed. It is within the composition and nano-morphology of the blended energetic layers (inks) that the corporate notes its added worth and secret of its trade. But that is not all: “We’re additionally engaged on compatibility between layers,” explains Sadok Ben Dkhil, the corporate’s chief know-how officer.
In the OPV Layer know-how developed by the corporate, every of the 4 layers is printed in a approach that optimizes the transport of prices within the supplies and within the remaining module. on the Valence plant, the clear room permits engineers and technicians to create these totally different layers that change into, in a approach, the “inks” used for manufacturing by inkjet printing.
The manufacturing software consists of an built-in electronics printing ecosystem. Much of the gear was bought from OPV’s former associate, Asca, which ceased manufacturing earlier than being taken over by Hering in Germany.
At the Dracula plant, the modules validated within the R&D laboratory are transferred to the pilot line for optimization. Then they go to automated manufacturing: The substrate cassette with the module design is positioned on the automated island the place it’s managed by the robotic, which successively locations it on the printing machines to obtain the corresponding layer of ink. The energetic layer wants time to stabilize, and every print should be adopted by a relaxation interval to permit solvent residues to dissipate. The printheads are geared up with nozzles a couple of micrometres in diameter that allow the ink droplets to be projected uniformly, creating exact patterns. The upkeep of those delicate units is on the coronary heart of the corporate’s industrial system.
Nanoelectronics means (at finest) zero defects, and that’s additionally the case exterior of the printing press. “Automation permits us to keep away from administration errors. Sometimes they aren’t seen to the bare eye throughout manufacturing, however at our scale of labor they’ll have an ideal affect on the aesthetic and technical results of the ultimate module ,” defined Dracula Technologies CEO Brice Cruchon. “Our objective is to automate all levels of the manufacturing line by the top of 2026 by incorporating improvements into our present course of.”
Another objective for the younger plant is to quadruple its manufacturing capability to 600 million sq. centimeters of modules by the yr 2026. To obtain this, Dracula plans to extend the variety of transfers , both in a number of shifts (morning and night, and even three shifts throughout peak. manufacturing durations) or by opening manufacturing on the weekend. It additionally intends to open new manufacturing strains. And there isn’t a scarcity of area. The firm moved to a 2500 sq. meters industrial space. Even previous greenhouses within the surrounding space might be transformed into new clear rooms for additional growth of manufacturing.
Finding the proper market: Replacement batteries, however not simply batteries
Dracula Technologies’ OPV modules have pure functions in on a regular basis battery-powered gadgets reminiscent of distant controls and smoke detectors. With an output of 61 to 72 µW for 100 lux (a low stage of complete gentle content material), the units are in a position to exchange batteries. This market is made extra accessible by the truth that the corporate has developed a versatile movie storage machine utilizing a layer know-how that’s straight built-in into the module by inkjet printing. Called LAYER®Vault, the know-how can provide vitality to a tool even when it has not been uncovered to gentle (complete darkness) for a brief time frame — a couple of hours, an evening.
Dracula has signed their first contract with COOLR for autonomous digital camera functions in fridge inventory administration. “We’re speaking about a number of hundred thousand gadgets a yr over the subsequent few years,” Cruchon stated.
Other functions are envisaged for the digital price ticket market within the retail sector, for product-integrated logistics monitoring tags for inventory administration, for instance, or for geolocation units for livestock, and even for good playing cards/chips (metro, ID card, and so forth.) to be acquired as a substitute of transmitters solely.
The inauguration of the Green Micro Power Factory introduced many potential prospects. Interest has been expressed in different sectors, however it’s too early to inform. Dracula Technologies at the moment has 40 workers. In 2026, it goals to have gross sales of €40 million and recruit virtually 100 folks, together with clear operators for manufacturing, course of and high quality engineers and folks devoted to the event of enterprise.
This content material is protected by copyright and will not be reused. If you wish to cooperate with us and wish to reuse a few of our content material, please contact: [email protected].
Popular content material
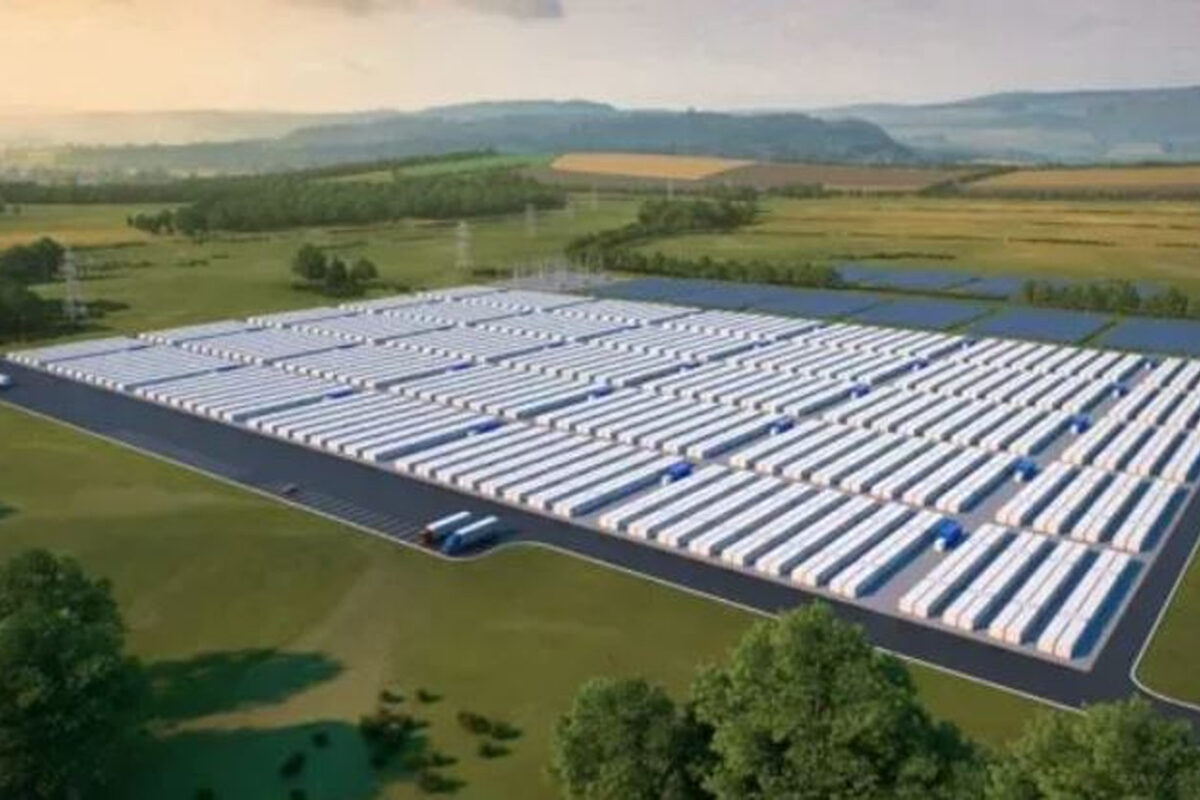
[ad_2]
Source link