[ad_1]
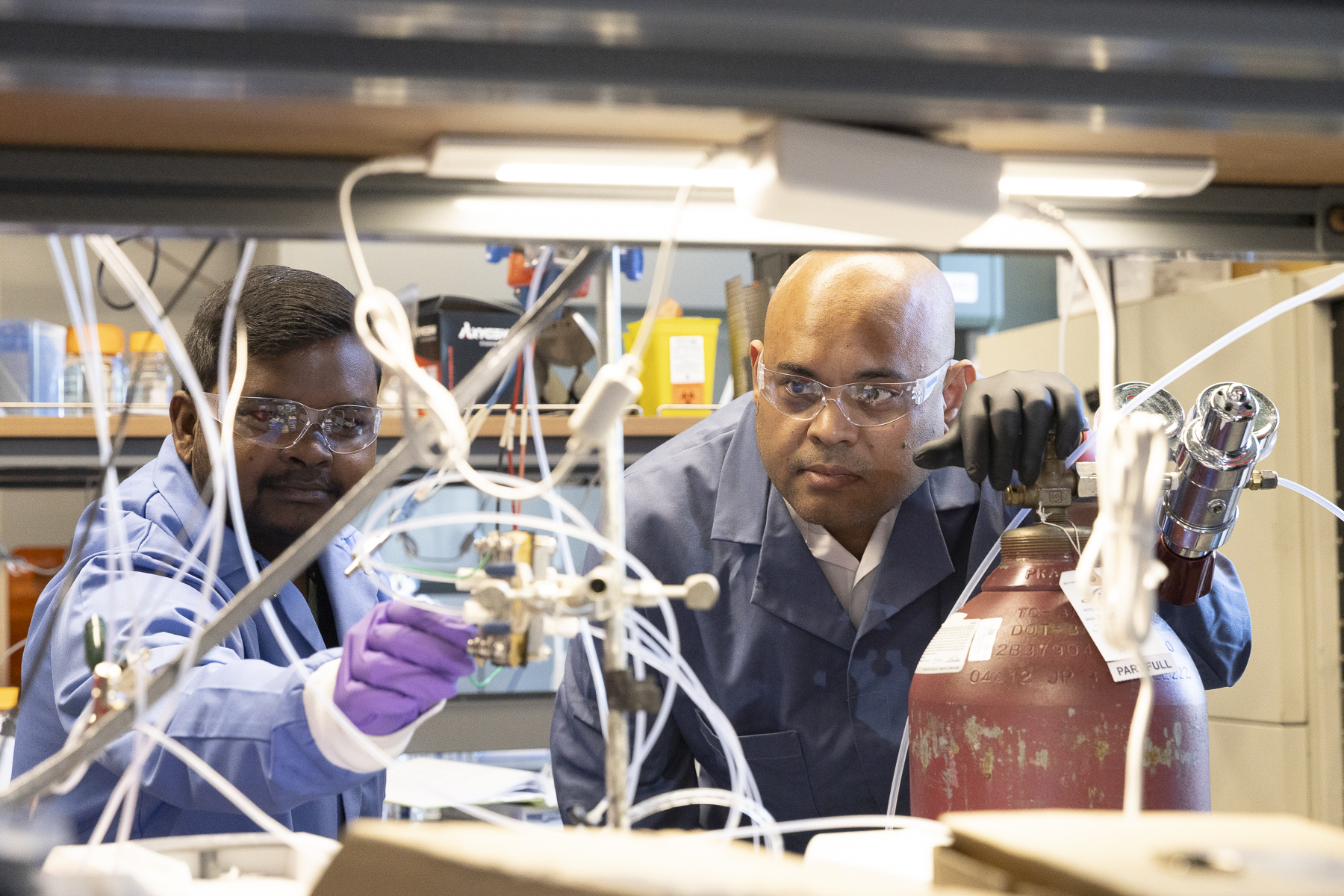
Engineers on the University of Illinois Chicago helped design a brand new methodology to supply hydrogen gasoline from water utilizing solely solar energy and agricultural waste, comparable to manure or husks. The methodology reduces the power required to extract hydrogen from water by 600%, creating new alternatives for sustainable, climate-friendly chemical manufacturing.
Hydrogen-based fuels are probably the most promising sources of fresh power. But producing pure hydrogen gasoline is an energy-intensive course of that usually requires coal or pure gasoline and huge quantities of electrical energy.
In a paper for Cell Reports Physical Science, a multi-institutional workforce led by UIC engineer Meenesh Singh revealed a brand new course of for inexperienced hydrogen manufacturing.
The methodology makes use of a carbon-rich substance referred to as biochar to scale back the quantity of electrical energy wanted to transform water into hydrogen. By utilizing renewable power sources comparable to solar energy or wind and extracting the byproducts for different makes use of, the method can scale back greenhouse gasoline emissions to web zero.
“We are the primary group to indicate that you may produce hydrogen utilizing biomass at a fraction of a voltage,” stated Singh, affiliate professor within the division of chemical engineering. “It’s a transformative know-how.”
Electrolysis, the method of splitting water into hydrogen and oxygen, requires electrical energy. On an industrial scale, fossil fuels are sometimes required to generate this electrical energy.
Recently, scientists lowered the voltage required for water splitting by introducing a carbon supply into the response. But this course of additionally makes use of coal or costly chemical substances and releases carbon dioxide as a by-product.
Singh and colleagues modified this course of to make use of biomass from widespread waste merchandise. By mixing sulfuric acid with agricultural waste, animal waste or sewage, they create a slurry-like substance referred to as biochar, which is wealthy in carbon.
The workforce experimented with various kinds of biochar comprised of sugar cane, hemp waste, paper waste and cow dung. When added to the electrolysis chamber, all 5 biochar varieties lowered the facility required to transform water to hydrogen. The finest performer, cow dung, lowered {the electrical} requirement sixfold to about one-fifth of a volt.
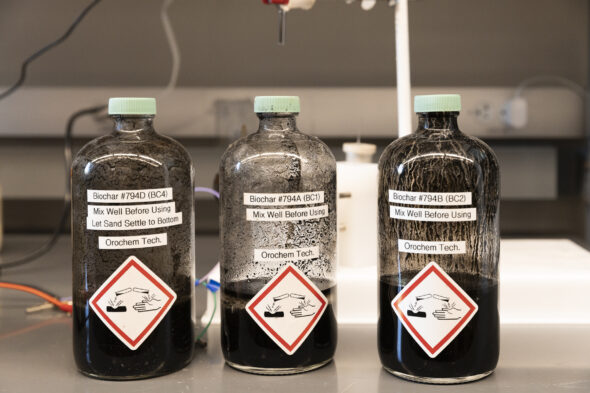
The power necessities are so low that the researchers have been in a position to react with a regular silicon photo voltaic cell that produces about 15 milliamps of present at 0.5 volts. That’s lower than the quantity of energy produced by a single AA battery.
“It’s very environment friendly, with round 35% conversion of biochar and photo voltaic power into hydrogen,” stated Rohit Chauhan, a co-author and postdoctoral scholar in Singh’s lab. “These are world document numbers; that is the very best that anybody has proven.”
To make the method net-zero, it should seize the carbon dioxide generated within the response. But Singh stated it might even have environmental and financial advantages, comparable to turning pure carbon dioxide into carbonated drinks or changing it into ethylene and different chemical substances used to make plastics. .
“This won’t solely diversify using biowaste however allow the clear manufacturing of assorted chemical substances past hydrogen,” stated UIC graduate Nishithan Kani, co-lead writer of the paper. “This low-cost technique to produce hydrogen might permit farmers to change into self-sustainable for his or her power wants or create new earnings streams.”
Orochem Technologies Inc., which is selling the analysis, has filed for patents on their processes for producing biochar and hydrogen, and the UIC workforce plans to check the strategies on a big scale.
In addition to Singh, Kani and Chauhan, the paper was co-authored by UIC graduate pupil Rajan Bhawnani. Other co-authors are from Stanford University, Texas Tech University, Indian Institute of Technology Roorkee, Korea University and Orochem Technologies Inc.
[ad_2]
Source link